1.概述
進(jìn)口紅土型氧化鎳礦,采用火法方式冶煉鎳鐵是近年來在國內(nèi)廣泛投資的冶金項(xiàng)目。在國內(nèi),目前大型鎳鐵冶煉企業(yè),一般采用回轉(zhuǎn)窯——礦熱爐的方法,生產(chǎn)品位在20% 以上的鎳鐵。紅土礦一般含鎳在2%左右,以生產(chǎn)20%鎳鐵為例,鎳金屬的綜合回收率按90% ,可知渣的產(chǎn)生量至少在9l%以上,渣的數(shù)量巨大,同時(shí)高溫液態(tài)渣蘊(yùn)含的熱量非常高,合理回收渣的能量對于鎳鐵冶煉的成本影響很大。
2.經(jīng)濟(jì)效益
某鎳業(yè)有限公司現(xiàn)有回轉(zhuǎn)窯—礦熱爐鎳鐵生產(chǎn)線15條,年產(chǎn)鎳鐵60萬噸,每條鎳鐵生產(chǎn)線每日排渣量234t/d,按運(yùn)轉(zhuǎn)率85%核算,平均每天排渣量為2993.5t/d。排渣溫度為1580℃,所蘊(yùn)含的熱量不僅數(shù)量大,且品質(zhì)高,利用價(jià)值,若渣冷卻溫度后為130℃,其每噸顯熱相當(dāng)于標(biāo)煤78kg。如對該熱量合理回收,回收率按照50% 計(jì)算,則相當(dāng)于每噸渣回收熱量11.455GJ,相當(dāng)于每噸渣節(jié)約標(biāo)煤39.08kg,每天節(jié)約標(biāo)煤116.61t/d,相當(dāng)于發(fā)電94.93萬kWh。
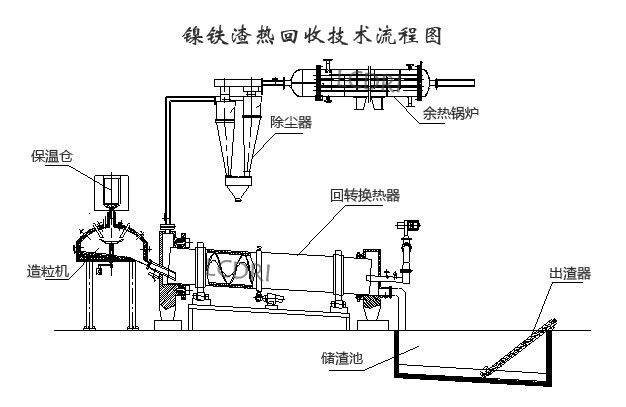
3.鎳渣處理的目標(biāo)
某鎳業(yè)有限公司目前鎳渣處理采用了熔融渣溜槽排放噴水冷卻的方法,耗水量大,現(xiàn)場環(huán)境差,熔渣蘊(yùn)含的熱能沒有回收。因鎳渣化學(xué)成分的限制,冷卻后的鎳渣用于路基修筑,是性能良好的筑路材料。
因此,對鎳渣處理主要應(yīng)實(shí)現(xiàn)三個(gè)目標(biāo):一是實(shí)現(xiàn)無水冷卻,節(jié)水并改善環(huán)境;二是冷卻后的鎳渣成為性能良好的筑路材料;三是實(shí)現(xiàn)高溫熔渣熱能的回收發(fā)電。
4 技術(shù)可行性
根據(jù)上述目標(biāo),就必須實(shí)現(xiàn)鎳渣的干法粒化工藝,目前在鎳鐵行業(yè)沒有資料表明開展了這方面的研究和應(yīng)用,為此可以借助和借鑒類似行業(yè),主要是鋼鐵行業(yè)相關(guān)的技術(shù)和成果。
干法冷渣即依靠高壓空氣實(shí)現(xiàn)熔融渣冷卻、粒化的工藝。針對濕法處理工藝的缺點(diǎn),20世紀(jì)70年代國外就已開始研究干式?;郀t渣的方法。前蘇聯(lián)、英國、瑞典、德國、日本、澳大利亞等國都有研究高溫熔渣(包括高爐渣、鋼渣等)干式粒化技術(shù)的記錄。有的方法還進(jìn)行了工業(yè)試驗(yàn),有影響力的主要有:滾筒法、風(fēng)淬法和離心?;ǎ@些方法均沒有在鎳鐵冶煉上應(yīng)用實(shí)踐。
4.1滾筒法
日本鋼管公司(NKK)在福山4號高爐試驗(yàn)的內(nèi)冷雙滾筒法。兩個(gè)滾筒在電動機(jī)帶動下連續(xù)反向轉(zhuǎn)動,帶動熔渣形成薄片狀粘附其上,滾筒中通入有機(jī)高沸點(diǎn)的流體工質(zhì),工質(zhì)吸收熔渣薄片的熱能后汽化,同時(shí)熔渣薄片冷卻后粘附在滾筒上,形成渣片以后要由刮板清除,有機(jī)液體蒸汽經(jīng)換熱器冷卻再次返回滾筒,回收的熱量用來發(fā)電。由于渣層薄,所以傳熱速度很快,因此該法的熱效率很高,熱回收率達(dá)77%。
但滾筒法設(shè)備處理能力不高、作業(yè)率低,不適合在現(xiàn)場大規(guī)模連續(xù)處理冶金渣,通常只能接受來自渣罐的熔渣,同時(shí)排渣溫度偏高,熱回收率低,凝固的薄渣片粘在滾筒上,必須用刮板刮下來,工作效率低并使設(shè)備的熱回收效率和壽命下降。
20世紀(jì)8O年代,日本的住友金屬公司曾經(jīng)建立了采用滾筒法處理高爐渣能力為40t/h的試驗(yàn)工廠。當(dāng)渣流沖擊到旋轉(zhuǎn)著的單滾筒外表面上時(shí)被破碎化,?;俾涞搅骰采线M(jìn)行熱交換,可以回收50% 一6O%的熔渣顯熱。
單滾筒工藝的缺點(diǎn)在于單筒的破碎粒化能力不足,造成渣粒的粒徑分布范圍太,導(dǎo)致在流化床上與換熱介質(zhì)的換熱面積小,換熱效率低,冷卻速度不足。
1995年,寶鋼購買了俄羅斯烏拉爾鋼鐵研究院在實(shí)驗(yàn)室規(guī)模內(nèi)研究開發(fā)的滾筒法液態(tài)鋼渣處理技術(shù)。經(jīng)過3年的技術(shù)轉(zhuǎn)化攻關(guān),于1998年5月在寶鋼三期工程的250t轉(zhuǎn)爐分廠,建成了世界上臺滾筒法處理液態(tài)鋼渣的工業(yè)化裝置。
高溫熔渣順著溜槽倒人滾筒時(shí),滾筒邊旋轉(zhuǎn)邊向筒內(nèi)急速噴淋,由于其內(nèi)部結(jié)構(gòu)特殊,不會引發(fā)爆炸,安全可靠。當(dāng)高溫爐渣進(jìn)入簡體,爐渣間分子聚合力較小,同時(shí)滾筒勻速旋轉(zhuǎn)時(shí),鋼渣與內(nèi)部鋼球介質(zhì)碰撞時(shí)被充分破碎,所以在較小能量碰撞下能將鋼渣破碎成較小顆粒,其中90%顆粒的粒徑在10mm 以下。應(yīng)用該裝置,寶鋼的鋼渣資源得到了綜合利用,但是鋼渣所蘊(yùn)含的能量沒有得到有效回收。
4.2風(fēng)淬法
利用循環(huán)空氣回收爐渣顯熱,通過余熱鍋爐以蒸汽的形式回收顯熱,稱為風(fēng)淬法。風(fēng)淬法常用于處理鋼渣。1977年, 日本鋼管公司(NKK)和三菱重工合作研發(fā)了風(fēng)淬?;墼@熱回收系統(tǒng),并于1981年末在福山制鐵所建成世界上套轉(zhuǎn)爐鋼渣風(fēng)淬粒化熱回收裝置,熔渣熱能回收率40~45% 。
由于鋼渣自身的性質(zhì),風(fēng)淬法處理鋼渣不考慮?;Aw含量的問題,而更關(guān)注熱能的回收。當(dāng)然,風(fēng)淬法也能應(yīng)用于高爐渣的處理。
新日鐵、日本鋼管、川崎制鐵、神戶制鋼、住友金屬和日新制鋼6家公司從1982年開始在新日鐵名古屋3號高爐上進(jìn)行了為期6年的風(fēng)淬法高爐渣干式?;囼?yàn) ,其主要性能為:渣處理量4Ot/h,蒸汽量7t/h,蒸汽參數(shù)1.5MPa/220℃ ,熱回收率65% ~79%。
風(fēng)淬法的缺點(diǎn)也是比較明顯的,由于空氣的比熱容比水要小,所以干燥?;^程中動力消耗很大、與水淬相比冷卻速度很慢。為了防止?;诠探Y(jié)之前粘結(jié)到設(shè)備表面上,還必須加大設(shè)備的尺寸,從而造成設(shè)備體積龐大、復(fù)雜,加工制造困難,而且造價(jià)高。
4.3 離心?;?br />
英國克凡納金屬公司(Kvaemer Metals)開發(fā)了一種轉(zhuǎn)杯?;瘹饬骰矡崮芑厥占夹g(shù)。熔渣通過覆有耐火材料的流渣槽從渣溝流至轉(zhuǎn)杯中心,在離心力作用下熔渣在轉(zhuǎn)杯的邊緣被?;?,然后渣粒在飛行中被冷卻,渣粒碰到粒化器內(nèi)壁時(shí)已經(jīng)足夠硬,不會粘到壁上,這一點(diǎn)因水冷壁的存在得以強(qiáng)化。
從裝置上方排出的氣流溫度可達(dá)400—600℃ ,在集氣罩上設(shè)有余熱回收系統(tǒng)。離心粒化法曾經(jīng)于20世紀(jì)80年代初期在英國鋼鐵公司Redes年產(chǎn)1萬t的高爐上進(jìn)行了為期數(shù)年的工業(yè)試驗(yàn)。
離心粒化法的設(shè)備簡單、動力消耗小、處理能力大、適應(yīng)性好、產(chǎn)品粒度分布范圍窄。離心粒化技術(shù)的原理與目前在鎳鐵冶煉領(lǐng)域使用的鎳鐵?;ㄊ窒嗨?,所不同的是鎳鐵流經(jīng)圓盤撞擊?;?,落人到?;氐乃壑校ㄟ^水將其進(jìn)一步冷卻,并通過水將其沖到振動篩上脫水、干燥。
根據(jù)鋼鐵研究總院對轉(zhuǎn)杯法試驗(yàn)結(jié)果:當(dāng)轉(zhuǎn)杯轉(zhuǎn)速為3000r/min,熔渣流量為2t/min時(shí),所需要的電機(jī)功率約為12~15kW ,能耗大大低于風(fēng)淬?;?。
鋼鐵研究總院2004年就已開始研究高爐渣急冷干式?;夹g(shù),對離心粒化與風(fēng)淬相結(jié)合的工藝也進(jìn)行過相關(guān)的實(shí)驗(yàn)。以離心力保證?;牧6确植肌oL(fēng)淬主要保證其降溫速率以控制玻璃體含量并輔助調(diào)節(jié)粒度分布,試驗(yàn)結(jié)果證明該方法具有粒化效率高、動力消耗低的優(yōu)點(diǎn)。
4.4現(xiàn)有技術(shù)的局限
目前高爐渣急冷干式粒化技術(shù)主要是結(jié)合鋼鐵行業(yè)需要開發(fā)的,其需要主要是三點(diǎn):一是爐渣中含有的渣鐵的回收,這一點(diǎn)要求熔渣?;瘯r(shí)粒度要盡量細(xì)碎,便于渣鐵的分離回收;二是熔渣的淬冷,以使熔渣中活性礦物盡可能多的保存下來,便于資源化利用;三是熔渣中蘊(yùn)熱的回收利用。
基于以上三點(diǎn),上述工藝用于鋼鐵行業(yè)內(nèi)高溫熔渣的干法?;强尚械?。在選擇鎳鐵渣的干法?;に嚂r(shí)可以參考,針對高溫鎳鐵渣冷卻處理要實(shí)現(xiàn)的三個(gè)目標(biāo),開發(fā)適合的?;に嚭蜔峄厥占夹g(shù)及裝備。
5.粒化設(shè)備
借鑒鋼鐵行業(yè)現(xiàn)有干法造粒工藝的思路,結(jié)合高溫鎳鐵渣冷卻處理要實(shí)現(xiàn)的三個(gè)目標(biāo),其核心問題在于開發(fā)出合適的高溫鎳鐵渣造粒設(shè)備,使其經(jīng)過初步換熱形成粒徑合適的固態(tài)渣,進(jìn)而對其進(jìn)行有效的熱回收。
5.1?;O(shè)備的技術(shù)原理
從高溫液態(tài)鎳鐵渣的物料特性出發(fā),其液相粘度很小,流動性很好,可以像水一樣流動,初始溫度為1580℃,蘊(yùn)含顯熱為2496kj/kg,其固化溫度約在1100℃,高溫液態(tài)鎳鐵渣由1580℃高液態(tài)轉(zhuǎn)化為固態(tài)過程中需要放出約758kj/kg的熱量,這些熱量通常需要有其它媒質(zhì)吸收,常用的媒質(zhì)一般是水、空氣及合適的固體材料等,可以采用單一或復(fù)合媒質(zhì)。當(dāng)采用水(25℃)、空氣(25℃)作為單一冷媒時(shí),對于每1kg1580℃的高溫鎳鐵渣冷卻到1100℃時(shí)其對應(yīng)的消耗量分別為0.31kg和2.92Nm3(空氣被加熱到200℃)。而當(dāng)采用冷態(tài)鎳鐵渣(130℃)作為單一冷媒時(shí),其用量為1.30kg(假定冷渣被加熱到平均500℃)。
考慮到換熱速率的問題,為使高溫液態(tài)鎳鐵渣盡量快的有液態(tài)轉(zhuǎn)化到固態(tài),就需要有效擴(kuò)大與冷媒的接觸面積和縮小粒徑或料層厚度。考慮到物料的終利用對物料粒度的要求及設(shè)備的開發(fā),冷卻的料層厚度應(yīng)保持在合適的范圍內(nèi)。
同時(shí)還需要考慮到高溫液態(tài)鎳渣在冷卻固化的過程中,其粘度會隨著溫度的下降增加、黏附,增加脫附困難。
綜上所述,干法?;に囘^程中,需要從冷媒的選擇、固化過程中物料分布狀態(tài)的控制、物料與設(shè)備接觸方式等方面綜合考慮選擇。
本方案擬采用空氣冷卻干法造粒工藝,并使物料與冷媒采用面接觸的方式,以實(shí)現(xiàn)物料的冷卻固化實(shí)現(xiàn)造粒,合理控制料層厚度,使物料與物料與空氣充分接觸,為熱量的回收利用和鎳渣的資源化利用創(chuàng)造條件。
獲取詳細(xì)方案:李工13937919268